About Us
Topaz Otomotive Industrial Coating Company is located in Agean Free Zone - Izmir that has established in 2016 by our founder Osman Musluoğlu as a result of his 40 years of experience in the coating industry.
Osman Musluoğlu is also the founder of Solvent Kimya that has designed and established dozens of coating plants in Turkey and also in the world.
Topaz Otomotive has been operating in an area of 2500 m² for 6 years serving to OEM companies as Tier 2 supplier with its responsive vision to people and environment by not utilising any prohibited materials, products and processes.
Topaz Otomotive is specialized in the industrial coating sector, and certified by BSI with ISO 9001: 2015 Quality Management System at the beginning of 2018, right after its establishment, and provides coating services such as zinc, nickel, and especially zinc-nickel with an advanced product quality planning (APQP) approach in process designs.
Topaz Otomotive operates with an average of 50 employees. Our aim is to produce high value-added products in Turkey and to train employees with this vision.
Topaz Otomotive embraces the vision of continuous development and continuous R&D in order to adapt to the developing and changing technology. With our young and dynamic employees, we are here to respond to the demands of our customers both with high quality and speed.
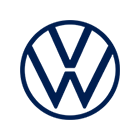
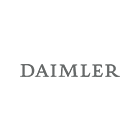
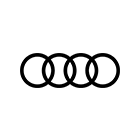
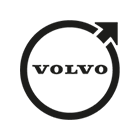
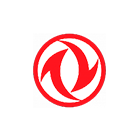
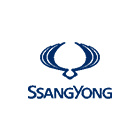
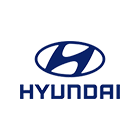
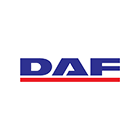
SERVICES
01
Alkali Zn-Ni Alloy Coating
02
Alkali Zn Coating
03
Salt Spray Test
04
Epoxy - Powder Painting
05
Plastisol (Liquid PVC) coating
Topaz Otomotiv was established on an area of 2500 m², since 2016, it has been performing Zinc Nickel (Zn-Ni) coating activity, which meets the ISO 19598 (former 50797) standard for the automotive industry as a Tier 2 supplier in the Automotive Industry standard in the Aegean Free Zone.
This standard
• Definitions to be used for coating systems.
• The minimum corrosion resistance to be obtained in the specified test procedures.
• Minimum required coating thickness.
• Describes the finishing processes after coating.
Zinc Nickel alloy plating is applied when conventional zinc plating processes fail to perform under high temperature and harsh environmental conditions. In today's conditions, it is the most preferred coating type, especially in the automotive sector. Nickel ratio is between 12-15%. In order to increase corrosion resistance, +3 valence passivation, organic or inorganic lacquer can be applied after coating. State-of-the-art X-Ray devices are used to measure the coating thickness and alloy ratio.
Zn-Ni coating is an electrolytic coating process. The component to be coated plays a cathode role as it is covered by the accumulation of Zn and Ni ions in the solution. This ion movement is provided by the electric current applied between the anode and the cathode.
Our processes; It is managed and designed with the Advanced Product Quality Planning (APQP) approach.
• Production Part Approval Process (PPAP)
• Failure Modes Effect Analysis (FMEA)
• Measurement Systems Analysis (MSA)
• Statistical Process Control (SPC)
Our company has been certified by BSI with the ISO 9001:2015 Quality Management System certificate.
Measurement, analysis and testing capabilities
• For coating thickness and Zn-Ni alloy ratio measurement; Fisher Scope XDL 230 X-Ray measuring instrument.
• Chemistry laboratory for volumetric analysis of chemical baths
• Salt Spray Test equipment with a capacity of 1000 lt and which meets BS EN ISO 9227 / ASTM B 117 standards for corrosion resistance tests.
• Available furnaces those can reach a temperature of 250°C to remove hydrogen embrittlement.
Other
Epoxy – Powder coating facility for the isolation of racks used in the coating process.
Plastisol (Liquid PVC) Coating for the isolation of racks used in the coating process.
• Definitions to be used for coating systems.
• The minimum corrosion resistance to be obtained in the specified test procedures.
• Minimum required coating thickness.
• Describes the finishing processes after coating.
Zinc Nickel alloy plating is applied when conventional zinc plating processes fail to perform under high temperature and harsh environmental conditions. In today's conditions, it is the most preferred coating type, especially in the automotive sector. Nickel ratio is between 12-15%. In order to increase corrosion resistance, +3 valence passivation, organic or inorganic lacquer can be applied after coating. State-of-the-art X-Ray devices are used to measure the coating thickness and alloy ratio.
Zn-Ni coating is an electrolytic coating process. The component to be coated plays a cathode role as it is covered by the accumulation of Zn and Ni ions in the solution. This ion movement is provided by the electric current applied between the anode and the cathode.
Our processes; It is managed and designed with the Advanced Product Quality Planning (APQP) approach.
• Production Part Approval Process (PPAP)
• Failure Modes Effect Analysis (FMEA)
• Measurement Systems Analysis (MSA)
• Statistical Process Control (SPC)
Our company has been certified by BSI with the ISO 9001:2015 Quality Management System certificate.
Measurement, analysis and testing capabilities
• For coating thickness and Zn-Ni alloy ratio measurement; Fisher Scope XDL 230 X-Ray measuring instrument.
• Chemistry laboratory for volumetric analysis of chemical baths
• Salt Spray Test equipment with a capacity of 1000 lt and which meets BS EN ISO 9227 / ASTM B 117 standards for corrosion resistance tests.
• Available furnaces those can reach a temperature of 250°C to remove hydrogen embrittlement.
Other
Epoxy – Powder coating facility for the isolation of racks used in the coating process.
Plastisol (Liquid PVC) Coating for the isolation of racks used in the coating process.